The concrete slab in a new facility exhibited excessive surface cracks. Testing Engineers was called in to determine the cause of this unsightly problem.
These cracks are somewhat circular in orientation, and occur at all column locations. There are also cracks radiating from these circular areas. The cracks themselves range from hairline thickness to 1/8"±, and exhibit random patterns and directions. None of the cracks observed exhibited any measurable vertical displacement.
The perimeter foundation has ties/dowels at 18" o.c., to tie the slab to the foundation. In addition, there are spread footings for the steel columns, approximately 8' x 8', squared to the exterior walls of the structure. There is no detail of how the slab is to be handled over these footings. An inspection of an adjacent tenant space provided a visual confirmation of the design details as they pertain to the slab, the perimeter foundation, and the column foundation pads. Reportedly, the shell of this structure was constructed under one contract, while the tenant improvement, including placement of the slab, was performed under a separate contract.
The cracking is the result of plastic shrinkage, which occurs when the rate of shrinkage in the concrete exceeds the strength gain. While shrinkage in concrete is inevitable, there are mix-design and structural design considerations that can minimize this problem. The photo shows a core through the full depth of the slab, with the crack progressing through the concrete paste towards the bottom. Note that the crack does not bisect the aggregate; rather it passes around the stone. When the concrete is still gaining strength, the bond between the aggregate and the cement paste is not strong enough to pull the aggregate itself apart.
The cracking of the slab around the steel columns may be attributed to a combination of joint placement and plastic shrinkage. If the joints immediately surrounding the column do not allow for shrinkage, the column will act as an anchor. As the slab shrinks, it pulls away from the column, leaving the corner "torn off". While it was originally thought that cracking might have been caused by pile-driving and/or adjacent demolition work, the type of crack found (and shown in the photo) is indicative of plastic shrinkage. Cracks caused by adjacent work would generally be through fractures as a result of differential settlement, impact, or bending. |
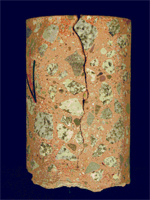
|