Corrosive Soils
Causes, Effects and Mitigation
By Hossein Arbabi
TESTING ENGINEERS, INC.
Soils, like any environment, can be corrosive. If we only used soil to plant flowers and trees, we probably wouldn't care too much – but as it stands, the dirt beneath our feet supports man-made structures of all kinds, and much of our utilities infrastructure is buried in it. While the effects of corrosive soil can cause structural failure and financial burden, mitigating measures taken into account during design and construction, as well as an understanding of the corrosive potential in a particular soil can minimize these issues.
The beginning of a construction project may involve excavation, fill, the addition of soil modifiers, dewatering - any number of processes that are meant to prepare the site for work. But what are the factors that contribute to the corrosive potential of soil? Aeration, moisture content (and/or time of wetness), temperature, pH, and resistivity are the primary telltales. The following is a more detailed description of the manner in which each of the above factors influences soil corrosivity.
Aeration – This is defined as the amount of air trapped within the soil. Aeration is an important factor in corrosion as it is a factor in water retention and evaporation rates. Well-aerated soil is more favorable from a (low) corrosivity standpoint because this generally leads to lower water retention and higher evaporation rates. The particle size and gradation within the soil plays a major role in determining the amount of aeration . Sandy soils are generally desirable, as the relatively large particles allow for better aeration, and facilitate faster evaporation rates after water has been introduced into the soil. A quick way to classify soils in terms of their aeration is by examining their color. Reddish, brown, or yellow soils indicate good aeration, while gray soil is indicative of poor aeration.
pH (acidity) - Soils can have a wide range of acidity, reaching anywhere from 2.5 to 10. As pH levels of 5 or below can lead to extreme corrosion rates and premature pitting of metallic objects, a neutral pH of about 7 is most desirable to minimize this potential for damage. The intrinsic pH level of a soil can also be affected by rainfall.
Moisture Content & Resistivity – Moisture content is a more important factor in soil corrosivity than any other variable. As water is one of the three components necessary for electrochemical corrosion (the other two being oxygen and metal), corrosion will not occur if the soil is completely dry. Experimental evidence dictates that an increased moisture content decreases resistivity of soils, in turn increasing their corrosive potential. Note that when the saturation point of the soil is reached, additional moisture has little or no effect on resistivity.
The relationship between the resistivity of the soil, a particular soil class, and the corrosion resistance for galvanized steel is summarized in the following table.
Soil Class |
Corrosion Resistance in
Galvanized Steel |
Electrical Resistivity, W-cm |
Sandy |
Excellent |
6,000 – 10,000 |
Loams |
Good |
4,500 – 6,000 |
Clay |
Fair |
2,000 – 4,500 |
Peat/muck |
Bad |
0 – 2,000 |
Conversely, the relationship between soil resistivity and corrosion potential in uncoated steel is shown in the table below.
Resistance Classification in Uncoated Steel |
Soil Resistivity,
W-cm |
Corrosion Potential |
Low |
0 - 2000 |
Severe |
Medium |
2000 - 10000 |
Moderate |
High |
10000 - 30000 |
Mild |
Very High |
>30000 |
None |
Temperature – temperature has an effect on soil resistivity and, as a result, corrosive potential. As soil temperature approaches 0° C, resistivity in the soil (for a given moisture content) increases gradually. However, as the temperature continues to decrease there is a rapid increase in resistivity with a corresponding decrease in the corrosive potential in the soil.
Other factors that can affect the corrosiveness of soils are levels of sulfates and salts. Generally soils are considered “mildly corrosive” if the sulfate and chloride levels are below 200 PPM and 100 PPM, respectively, for soils with pH levels of between 5 and 10, and resistivity greater than 3000 ohm-cm.
CASE STUDY
Introduction
We have all seen the news stories about a water main break – they always occur at some major intersection right at rush hour! Traffic is tied up. Business is lost, millions of gallons of water wasted, and thousands upon thousands of dollars spent repairing the damage. Our underground utilities are constantly under attack from corrosion, and in some instances failures are a combination of corrosion and external forces. The following case study describes the failure investigation of buried cast iron pipe that had cracked due to such a combination.
Leaks were discovered coming from an underground 8” diameter cast iron pipe that had been installed 15 years ago. To remedy the situation, 40 feet of pipe was removed and replaced. The typical operating pressure of the pipeline was reported to be 125 psi. Three pipe fragments were submitted to our laboratory for evaluation. A sample of the soil from an area adjacent to the pipe was also submitted.
Observations
The pipe fragments were visually examined and photographed in our laboratory. Shown below are overall views of the interior and exterior of a typical section, photos 1 and 2, respectively. The dark patches on the exterior of the pipe represent a form of corrosion specific to cast iron known as graphitization. This will be discussed in more detail in the next section. The chemical composition and microstructure of the pipe material was analyzed and found to be consistent with cast iron with typical levels of porosity.
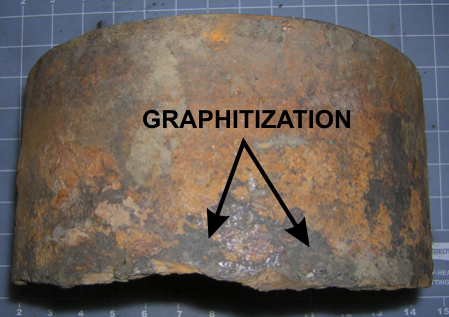
Photo 1 Photo 2
Photo 3 is a magnified view of the exterior of the pipe. This shows the extent of metal loss adjacent to the fracture surface. It is evident from the visual observations that the metal loss is confined to the exterior of the pipe, while the interior exhibited evidence of only mild to moderate corrosion. |
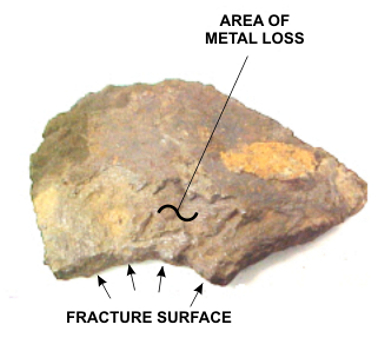
Photo 3 |
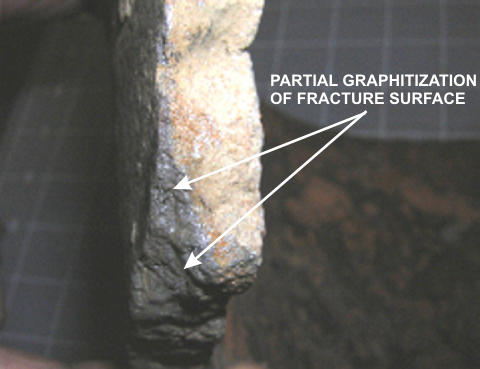
Photo 4
A typical fracture surface with severe loss of pipe wall thickness due to graphitization corrosion is depicted in Photo 4. A rough-polished cross section with the same type of corrosion through the entire pipe wall (dark area denoted with arrow) is presented in Photo 5.
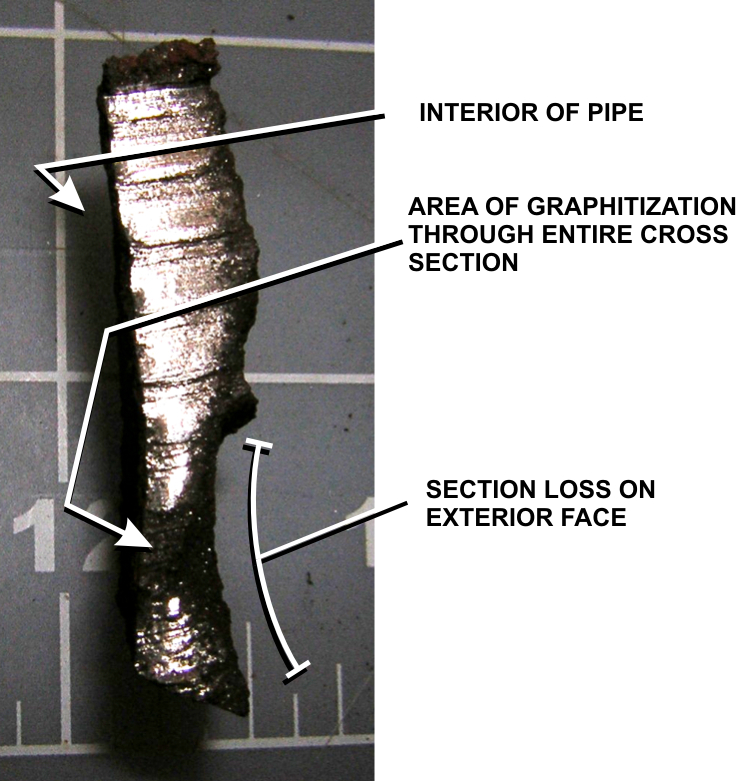
Photo 5
As the primary corrosion and subsequent section loss was external, the properties of the soil with respect to corrosivity were examined. The soil sample had a grayish appearance, indicative of poor aeration and potentially high corrosivity. Direct measurement of the soil's pH showed a value of 4.5, indicating an acidic soil. In addition, direct resistivity tests of the soil using the “Wenner four-pin” method indicated a resistivity value of 1800 W-cm, putting the soil in a corrosive category.
The analysis of the corrosion deposits on the outside of the pipe by Energy Dispersive X-ray (EDX) showed a high concentration of sulfur in addition to smaller amounts of chlorine. Photo 6 is a typical EDX spectrum representing all the elements found.
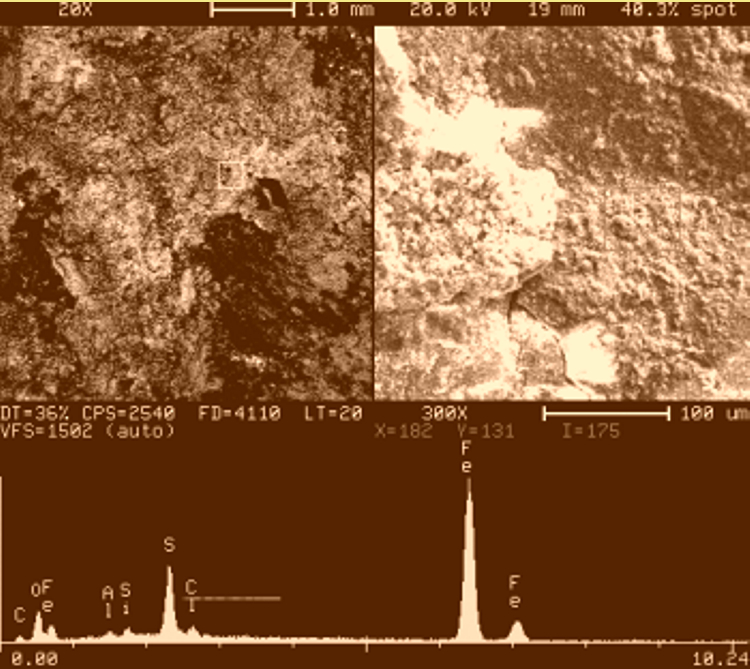
Photo 6
Discussion
The corrosion mechanism itself is of interest. Gray cast iron is used for pipes due to it's inherent resistance to corrosion. This resistance is due largely to the graphite matrix that forms during the casting process, and is interwoven with a matrix of pure iron. Graphitization corrosion occurs when the iron surrounding the graphite is attacked. The porous graphite matrix is left intact as black patches on the surface of the pipe. This corrosion mechanism, which is specific to gray cast iron, may give the false appearance of a structurally sound material. Unfortunately, the porous graphite has little strength, and makes the pipe prone to cracking under low external stresses.
As stated earlier, (graphitization) corrosion in a soil environment is a function of aeration, moisture content, temperature, pH, and resistivity. Dissolved constituents in the soil may also contribute to corrosion rates. In this instance, the measured low resistivity and low pH are consistent with a corrosive soil. Once a leak started, the moisture content in the soil would rise, greatly increasing the corrosive potential of the environment. In addition, the sulfur present on the exterior surfaces of the pipe section is a strong indication that corrosion is also microbiologcally influenced. The sulfur or sulfur compounds in the soil can support the growth of sulfate reducing or sulfur oxidizing bacteria that can in turn create the chemical conditions that can cause graphhitization.
As is the case with atmospheric corrosion, the extent of damage due to soil issues may be vastly different within relatively close quarters. This can be due to site-specific conditions in the soil allowing for differential drainage, aeration, acidity, and/or resistivity.
Conclusion
The chemistry of the fragments are typical of cast iron piping material, so material defects are not the likely cause of the failures. Cast irons are brittle by nature and are more fracture sensitive than wrought materials. Based on the significant corrosion and material loss on the exterior of the pipe, the fracture most likely initiated at an area of reduced cross-section, and may have been caused by internal (water pressure) forces, or by some external force including, but not limited to, nearby construction activity, expansion and contraction of the soil, erosion and/or settlement of the soil surrounding the pipe.
Recommendation
There are several methods of preventing corrosion of buried pipes, though most of these methods are only practical for application prior to installation of the piping. For existing buried pipes the most cost-effective method of minimizing or eliminating corrosion is cathodic protection. Cathodic protection involves the use of sacrificial magnesium or zinc anodes connected to the pipe material, which acts as the cathode. Under corrosive environments, the anode will corrode, sparing the cathode (pipe material). Both the replacement pipe sections and existing pipes can be effectively protected by this method.
We recommended that our client contact a firm that specializes in cathodic protection of buried pipes for preventing further corrosion.
HArbabi AT testing DASH engineers.com
|